Flow Reactors for Flow Chemistry Manufacturer, Exporter
Flow Reactors for Flow Chemistry Manufacturer, Exporter
Advantages of continuous flow production
The advantages of Continuous Flow Production of fine chemicals when compared to
traditional Batch Chemistry are :
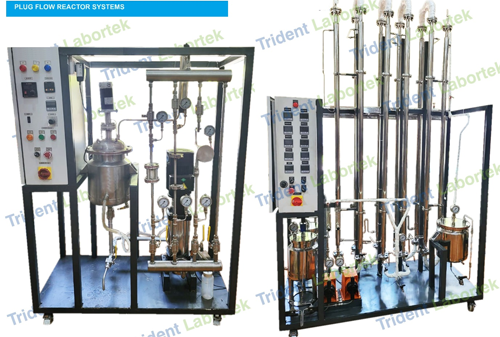
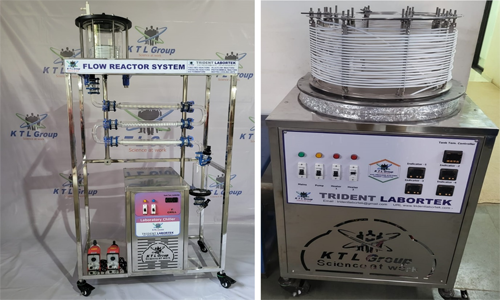
Safer reactions when handling hazardous materials
The high surface area to volume ratio of flow reactors provides improved heat removal. This ensures that highly exothermic reactions can be safely controlled. Continuous Flow Production allows small amounts of hazardous intermediate to be formed at any instant and then reacted to achieve the desired (and less hazardous) product. The inventory of hazardous material being processed at any one time can be minimized in flow when compared with batch.
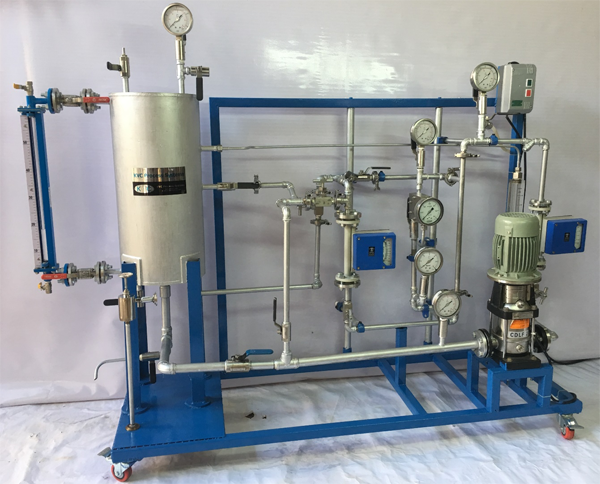
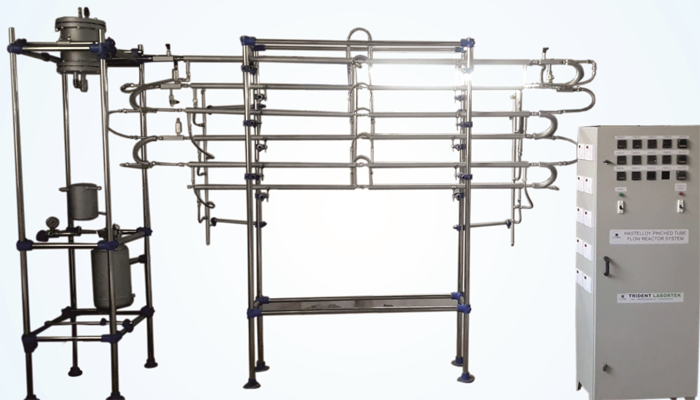
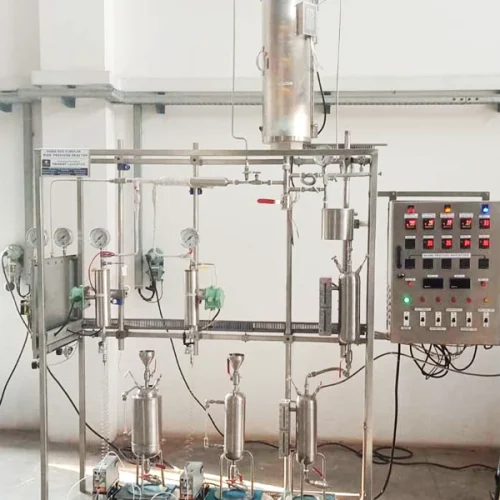
Safer reactions involving gas evolution
Reactions that evolve gas are much safer if flow as the maximum rate of gas evolution is limited by the rate at which the reagents are pumped. In batch reactors where all of the reactants are present at the same time, should the reaction “run away” then the rate of gas evolution can be uncontrolled possibly resulting in an explosion.
Safer reactions at high pressures
Flow reactors do not require a head space. The pressure within the reactor is controlled by a device called a back pressure regulator (BPR) and not by pressurizing the gas within the headspace as with traditional batch reactors. This eliminates the hazard associated with a volume of high-pressure compressed gas/vapour.
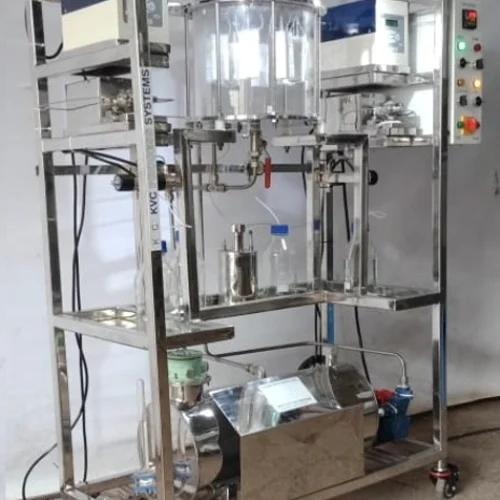
Reaction conditions simply not possible in batch reactors
Reaction times in Continuous Flow Production can be precisely controlled down to a few seconds or less, allowing the rapid generation of reactive intermediates to be reacted immediately in another reaction step. Multistep, telescoped reactions provide a route to complex organic transformations avoiding the steps of isolating intermediates.
Faster reactions
Flow reactors can be easily and safely pressurized & can achieve reactor pressures of Up to 200 bar). This allows reaction temperatures well above the normal boiling point of the solvents (e.g. liquid phase reactions with ethanol at 250 C) providing reaction rates 1000s times faster than under reflux conditions.
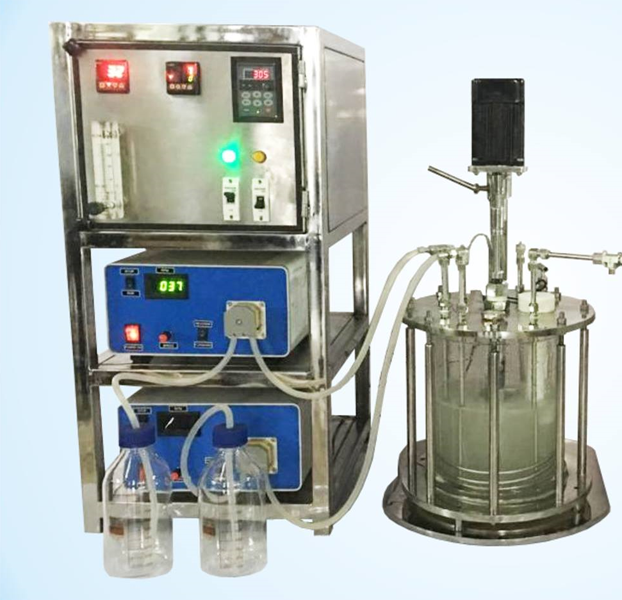
Rapid route to scale-up
The difficulties of scaling up batch reactions are well documented. Continuous Flow Production can be scaled up much more easily, simply by running for longer or by using higher flow rates and correspondingly larger reactors. However, the requirements for mass transfer and heat transfer in the larger reactors must be considered.
Rapid route to scale-up
The difficulties of scaling up batch reactions are well documented. Continuous Flow Production can be scaled up much more easily, simply by running for longer or by using higher flow rates and correspondingly larger reactors. However, the requirements for mass transfer and heat transfer in the larger reactors must be considered..
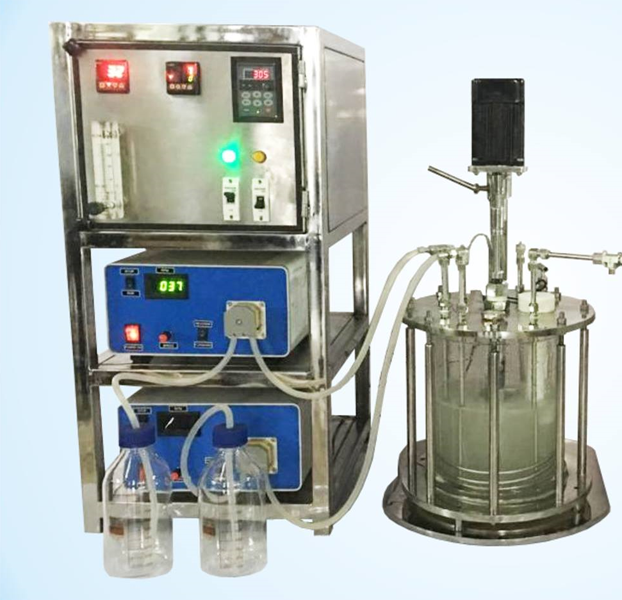
Integration of downstream processes
Downstream processes, work-up, and analysis can be integrated into the flow process. Operations such as aqueous workup, metal scavenging columns, or ion exchange resins can be added to the flowing process. Online analytical techniques of UV, conductivity, PH, and even FTIR can be easily implemented. Offline techniques such as LC / MS can be integrated either through automated fraction collection or using a sampling valve / dilutor for approaching real-time analysis..
Photochemical reactions in continuous flow production
Traditional batch photochemical reactors have limitations, particularly when scaling up photochemical reactions. Combining continuous flow with Photochemistry provides a powerful synthetic tool for accessing reaction pathways utilizing singlet and triplet states. The key benefits of continuous flow are; the product of the reactions are removed from the irradiated area, problems of photon penetration depth and mixing can be largely avoided, and reactions are safer as the volume of solvent in proximity to a hot lamp is significantly reduced.
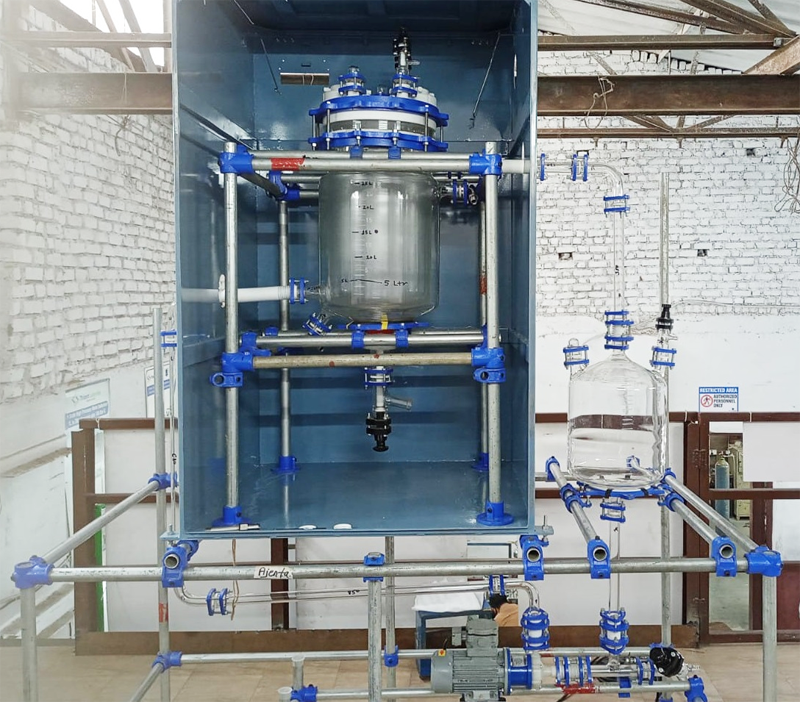